Power Chuck Manufacturer
Product Details
Model | DK415 |
Thru Hole Dia. [mm] | 117.5 |
Plunger Stroke [mm] | 23 |
Jaw Stroke Dia. [mm] | 10.6 |
Max RPM [r.p.m.] | 1800 |
Max Draw Bar Pull Force [kgf(kN)] | 5400(53) |
Max Gripping Force [kgf(kN)] | 13600(134) |
Max. Hydraulic Pressure [kgf/cm2(MPa )] | 19(1.9) |
Weight [kg] | 111.5 |
Matching Cylinder | / |
Gripping Range[mm] | Φ63~Φ381 |
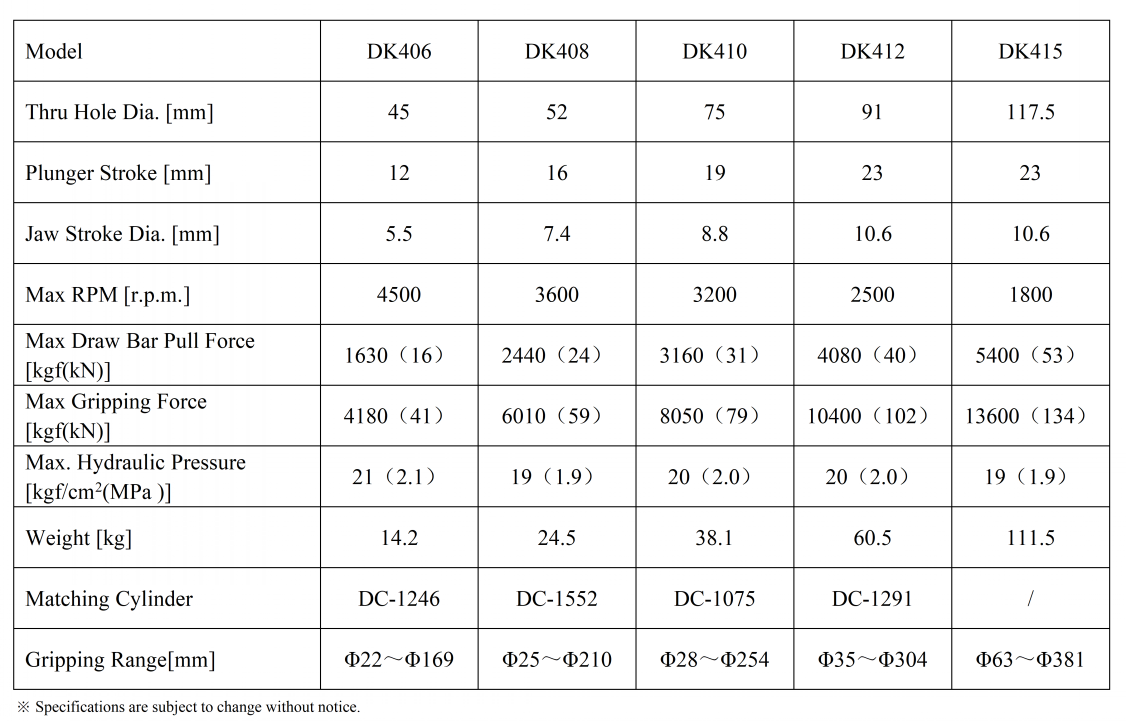
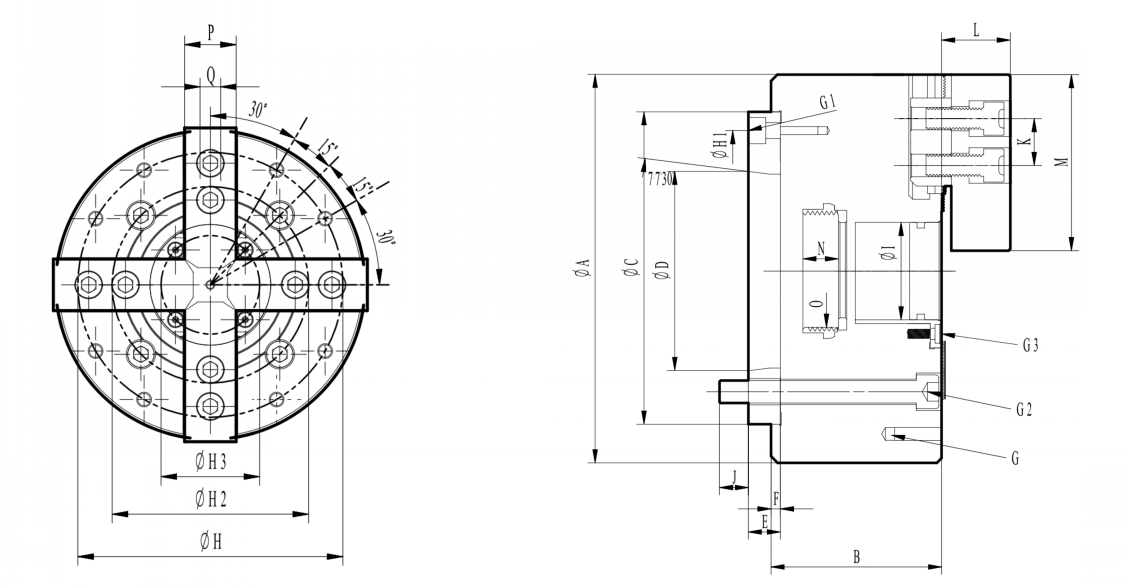
Model | DK415 |
Spindle Nose No. | A2-11(A2-8) |
A | 381 |
B | 133 |
C(h6) | 300 |
D | 196.87 |
E | 25 |
F | 6 |
G | 4-M12X1.75P |
G1 | 3-M8 |
G2 | 4-M20X2.5P |
G3 | 4-M6 |
H | 324 |
H1 | 260 |
H2 | 235.0 |
H3 | 155 |
I | 117.5 |
J | 28 |
K | 43 |
L | 66 |
M | 165 |
N | 42.5 |
O | M130X2P |
P | 62 |
Q | 22 |
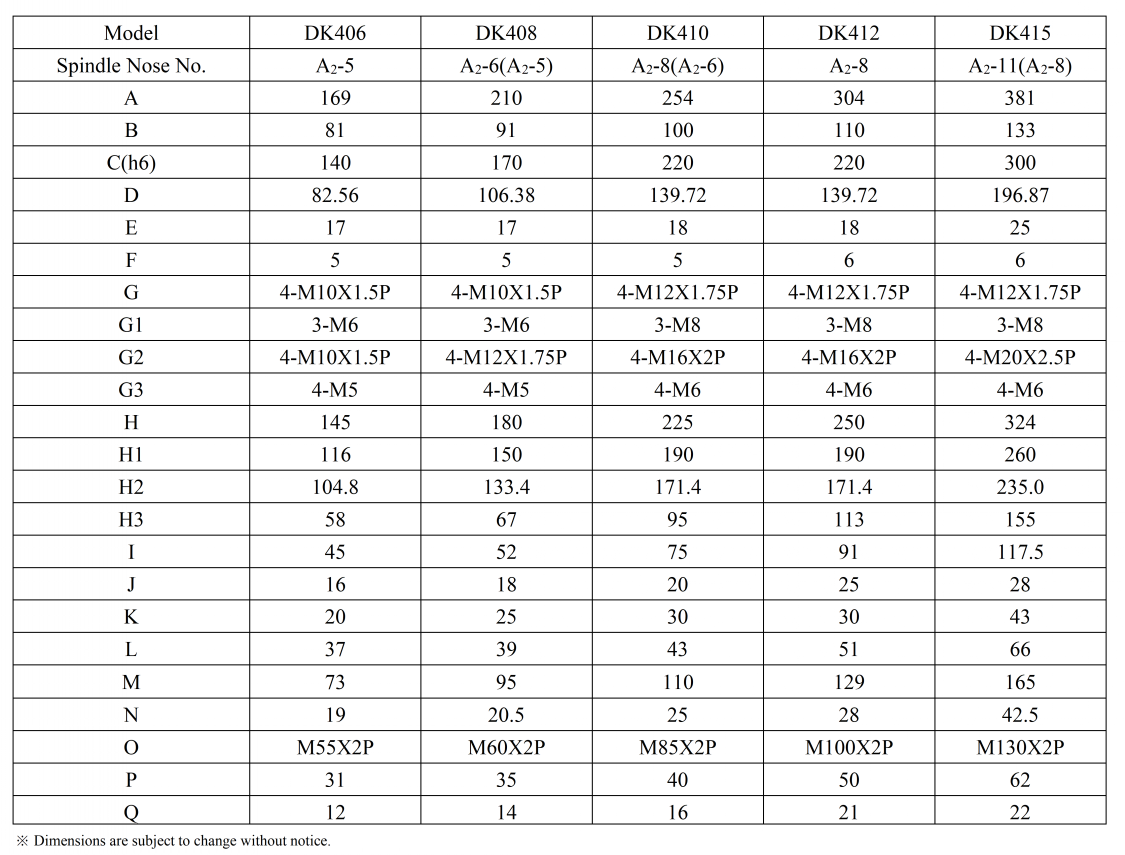
What are the key components of a power chuck?
The key components of a power chuck include:
Chuck Body: The chuck body is the main housing that holds the other components of the power chuck. It provides the structure and stability for the chuck and is typically mounted on the machine tool's spindle.
Jaws: Jaws are movable components that grip the workpiece during machining operations. They can be configured in different numbers (e.g., 2-jaw, 3-jaw, 4-jaw) and designs to accommodate various workpiece shapes and sizes.
Base Jaw: The base jaw is a fixed jaw that provides a stable reference point for gripping the workpiece. It is usually mounted on the chuck body and works in conjunction with the movable jaws to secure the workpiece.
Actuator: The actuator is the mechanism responsible for opening and closing the jaws to clamp or release the workpiece. It can be powered hydraulically, pneumatically, or electrically, depending on the type of power chuck.
Clamping System: The clamping system includes components such as pistons, cylinders, and pressure systems that apply force to the jaws to grip the workpiece securely. The clamping system ensures that the workpiece remains stable during machining operations.
Control System: The control system regulates the operation of the power chuck, controlling functions such as clamping force, jaw movement, and synchronization. It can be manual or automated, depending on the level of precision and control required.
Lubrication System: A lubrication system is often incorporated to reduce friction and wear between moving parts of the power chuck, ensuring smooth operation and prolonging the chuck's lifespan.
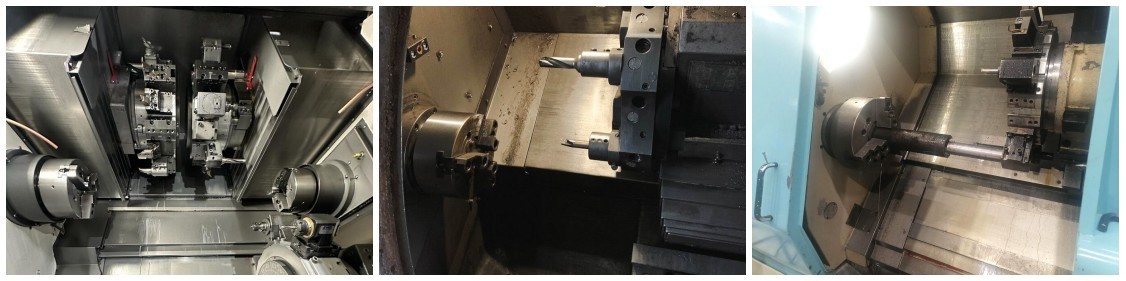
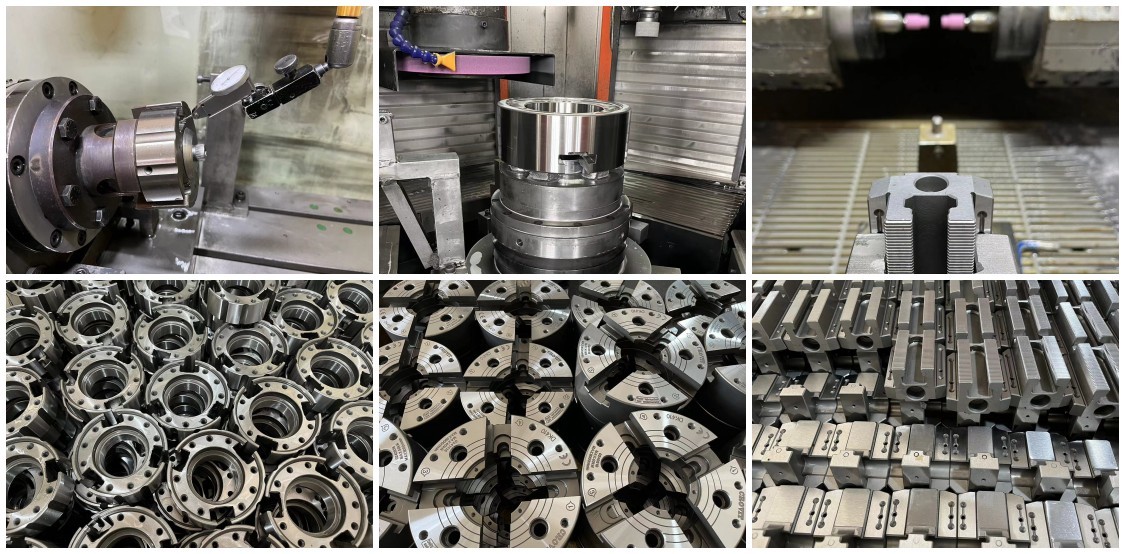
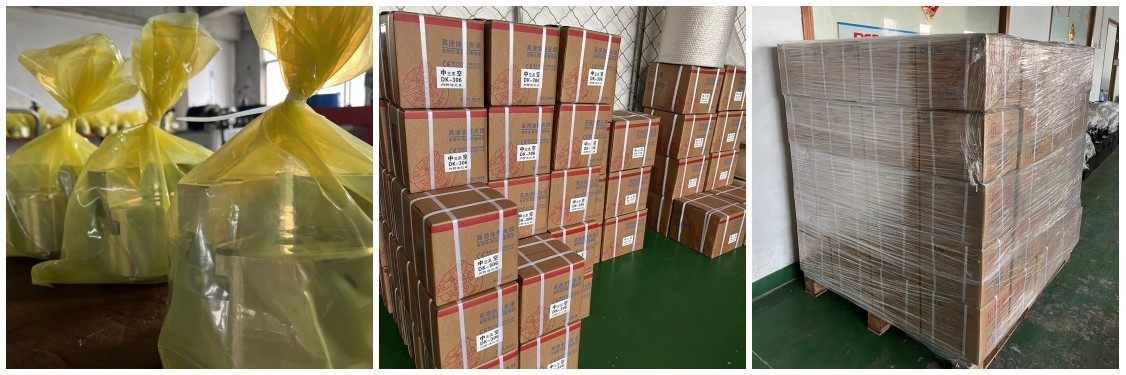
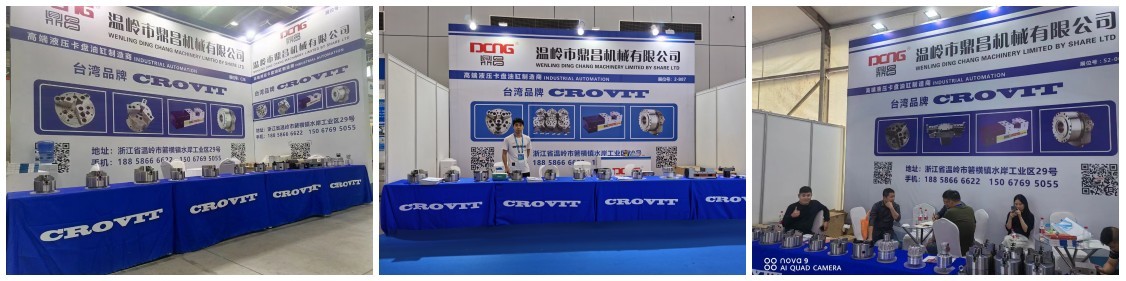
RELATED PRODUCTS
A hydraulic chuck tool holder is a type of tool holder that uses hydraulic pressure to securely hold cutting tools in place during machining operations, which is commonly used in CNC machining centers and other high-precision machining applications.
A hydraulic chuck is a type of workholding device commonly used on CNC lathes for securely gripping and holding workpieces during machining operations.
A power chuck is a type of workholding device commonly used in machining operations to securely grip and hold workpieces during turning, milling, drilling, or grinding processes. They are typically used on CNC lathes, machining centers, and other machine tools.
Hydraulic lathe chucks are commonly used in CNC lathes and other precision machining equipment to provide a strong and reliable grip on workpieces, ensuring stability and accuracy during turning, milling, drilling, or grinding processes.
GET A FREE QUOTE